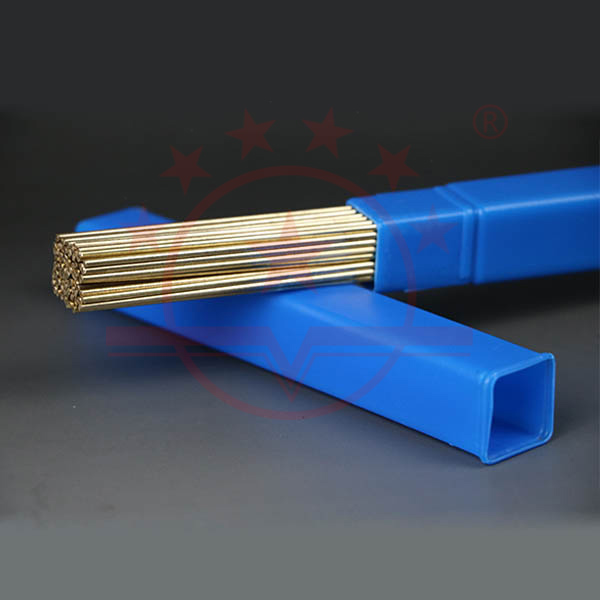
Factors affecting weldability
Weldability is a kind of technological property of metal materials.In addition to the properties of the material itself, it is also affected by the technological conditions, structural conditions and conditions of use.
(1) material factors
Materials include base material and welding material.Under the same welding conditions, the main factor that determines the weldability of the base material is its physical and chemical properties.
Physical properties, such as melting point, thermal conductivity, linear expansion coefficient, density, heat capacity and other factors, all affect the thermal cycle, melting, crystallization, phase transformation and other processes, thus affecting the weldability.Pure copper has high thermal conductivity, heat loss is rapid during welding, the range of temperature rise is very wide, groove is not easy to melt, welding needs intense heating.If the power of the heat source is insufficient, the defect of insufficient fusion will be produced.Copper, aluminum and other materials of high thermal conductivity, melting pool crystallization fast, easy to produce pores.Titanium, stainless steel and other materials with low thermal conductivity, welding temperature gradient, high residual stress, deformation.Moreover, because of the long residence time at high temperature, the grain in the heat-affected zone grows, which is bad for the joint performance.The linear expansion coefficient of aluminum and austenitic stainless steel is large.The density of aluminum and its alloy is small, when welding, the bubble in the pool and non-metallic debris is not easy to float and escape, will remain in the weld hole and slag.
Chemical properties, mainly to see the metal and oxygen affinity strength.Such as aluminum, titanium and their alloys have strong chemical activity.It is easy to oxidize under high temperature welding.Some metals are very sensitive to hydrogen, nitrogen and other gases. When welding, it is necessary to have reliable protection, such as inert gas protection welding or welding in vacuum.Otherwise, welding is difficult to achieve.
If it is a heterogeneous metal welding, only the physical and chemical properties and crystal structure of the metal is relatively easy to achieve welding.For the welding of steel, the main factor affecting the weldability is the chemical composition.The most influential elements are carbon, sulfur, phosphorus, hydrogen, oxygen and nitrogen.Other alloying elements, such as manganese, silicon, chromium, nickel, aluminum, titanium, vanadium, niobium, copper and boron, all increase the hardening tendency and crack sensitivity of the welded joint to different degrees.Therefore, the weldability of steel always deteriorates with the increase of carbon content and alloying element content.
In addition, the melting, rolling, heat treatment and microstructure of steel have different effects on weldability.Therefore, in recent years, a variety of CF steel (crack resistant steel), z-direction steel (laminar tear resistant steel), TMCP steel (controlled rolling steel) and so on have been developed and developed, which is to improve the weldability of steel by means of refining and refining grain and controlled rolling process.
Welding materials directly participate in a series of chemical metallurgical reactions in the welding process, which determines the composition, structure and properties of weld metal
And the formation of defects.If the choice of welding material is not appropriate, and the base material does not match.Not only can not meet the requirements of the use of the joint, but also will cause cracks and other defects and the change of microstructure performance.Therefore, the correct selection of welding materials is also an important metallurgical condition to ensure the quality of welded joints.
(2) technological factors
Process factors include welding method, welding process parameters, welding sequence, preheating, post heat and post heat treatment.Welding method has a great influence on weldability, which is mainly reflected in the characteristics of heat source and protection conditions.
The heat sources of different welding methods vary greatly in power, energy density and maximum heating temperature.Metal welding under different heat sources will show different welding properties.For example, electroslag welding has a high power rate, but a low energy density, and the highest heating temperature is not high.As a result, the grain size and impact toughness in the thermal affected zone are greatly reduced.It must be normalized before improvement can be made.On the contrary, electron beam welding, laser welding and other methods, the power is not large, but the energy density is high, heating quickly.The high temperature residence time is short, the heat-affected zone is very narrow, and there is no danger of grain growth.
The welding heat cycle can be adjusted and controlled by adjusting welding process parameters, preheating multilayer welding and controlling interlayer temperature and other process measures, so as to change the weldability of metal.For example, when welding some high strength steels with hardening tendency, the material itself has a certain cold crack sensitivity.When the process selection is not proper, the welded joint may produce cold cracks or reduce the joint's plasticity and toughness.If appropriate filling materials are selected, reasonable welding heat cycle is adopted, and pre-welding preheating or post-welding heat treatment measures are taken.It is completely possible to obtain a welded joint without crack defect and meeting the performance requirements.
(3) structural factors
It mainly refers to the design form of welded structure and welded joint, such as the influence of the structural shape, size, thickness, groove form, weld layout and section shape on weldability.The influence is mainly reflected in the heat transfer and the state of force.The heat transfer direction and velocity of different plate thickness, joint form or groove shape are different, which affect the crystal direction and grain growth.The shape of the structure, the thickness of the plate and the arrangement of the weld, etc., determine the stiffness and constraint degree of the joint, and affect the stress state of the joint.Poor crystalline morphology, severe stress concentration and excessive welding stress are the basic conditions for forming welding cracks.It is an important measure to improve weldability to reduce joint stiffness, cross weld, avoid excessive density of weld and reduce various factors that cause stress concentration.
(4) conditions of use
It refers to the working temperature, load condition and working medium of welded structure during service.These working conditions and operating conditions require the welding structure to have the corresponding performance.For example, welded structures working at low temperatures must have brittleness resistance.The structure working at high temperature should have anti-creep property.The structure working under alternating load has good fatigue resistance.Welding vessels working in acid, alkali or salt media should have high corrosion resistance and so on.In a word, the more severe the use conditions are, the higher the quality requirements are on the welded joint, and the more difficult it is to guarantee the weldability of the material.