Tungsten-arc welding is a welding using argon as shielding gas.Through an arc between the tungsten electrode and the welding body, the welding material itself is heated and melted (and melted when filler metal is added) to form the welding metal.Tungsten electrodes, molten pools, arcs and arc-heated joint areas are free from air pollution by argon.
During argon arc welding, the relative positions of the welding gun, filler metal and welding parts are as follows:
The arc length is generally 1-1.5 times the diameter of the tungsten electrode.
When the welding stops, the filler metal is first extracted from the pool (adding the filler metal according to the thickness of the welding piece), and the hot end still needs to be kept under the protection of the argon stream to prevent oxidation.
1. Welding gun (welding gun)
The tungsten-electrode argon arc welding gun (also known as a welding torch) not only clips the tungsten electrode and delivers welding current, but also ejects shielding gas.High current welding gun length time required to use water - cooled welding gun.Therefore, the correct use of welding gun and its protection is very important.
Tungsten electrode load current capacity (A)
Tungsten electrode diameter (mm) pure tungsten thorium tungsten cerium tungsten
Phi 1.0 20-60 15-20, 80-80
Phi 1.6 40, 50-160-100, 70-150
Phi 2.0 60-150 100-200100-200
Phi is 3.0, 140-180, 200-300
Phi is 4.0, 240-320, 300-400
Phi is 5.0, 300-400, 420-520
2. The routes
Gas is transferred to components such as argon cylinder pressure relief valves, flow meters, hoses and solenoid air valves (inside the welder).Pressure relief valves are used to reduce pressure and regulate the pressure of the shielding gas.Flow gauges are used to calibrate and adjust the flow of protective gas.Argon arc welding machine usually adopts the combined pressure relief pressure gauge, so it is convenient and reliable to use.
3. Argon purity
The purity of the material must be achieved during argon arc welding
The metallic material chrome-nickel stainless steel is too refractory metal
Argon purity (%) ≥99.7 ≥99.98
4. Specification parameters
The specification parameters of argon tungsten arc welding mainly include current, voltage, welding speed and argon flow rate.Its value depends on the type of material to be welded, the thickness of the plate, and the type of joint.For other parameters, such as the length of the tungsten electrode extending out of the nozzle, generally take 1-2 times of the diameter of the tungsten electrode, generally take less than 1.5 times of the diameter of the tungsten electrode, the distance between the tungsten electrode and the welding piece (arc length), nozzle size, etc.It is selected after the welding current value is determined.Specification for argon arc welding of stainless steel is as follows:
Welding current (A) argon flow (l/min) wire diameter
Dc positive connection 0.530-50 4 1.0
30-50 4 phi is 1.0 0.8
4 phi 1.6 1.0 35 to 60
Phi is 1.5 1.6 45-80-4-5
75-120-5-6 phi is 2.0 2.0
Phi is 3.0 to 2.0 6-7, 110-140
Weld surface color and gas protection effect
The welding material had better be good than bad
Stainless steel silver white, golden blue red gray black titanium alloy bright silver orange yellow blue purple blue gray white titanium oxide powder
6. Clean before welding
Argon tungsten arc welding is very sensitive to the contamination of welding parts and filler metal surfaces, so grease, coating, processing lubricant and oxide film must be removed from the welding parts before welding.
7. Safety technology
Argon tungsten arc welding operators, must wear a good head mask, gloves, wear work clothes, work shoes, to avoid electric arc in the ultraviolet and infrared burns.
Stell tungsten argon arc welding machine is equipped with high frequency arc initiator, although the low power high frequency high voltage will not operate, but when the insulation performance is poor, high frequency electricity will burn the operator's hand skin, and it is difficult to cure, so the insulation performance of welding handle must be often checked.
During tig welding, ventilation in the welding area should be enhanced.
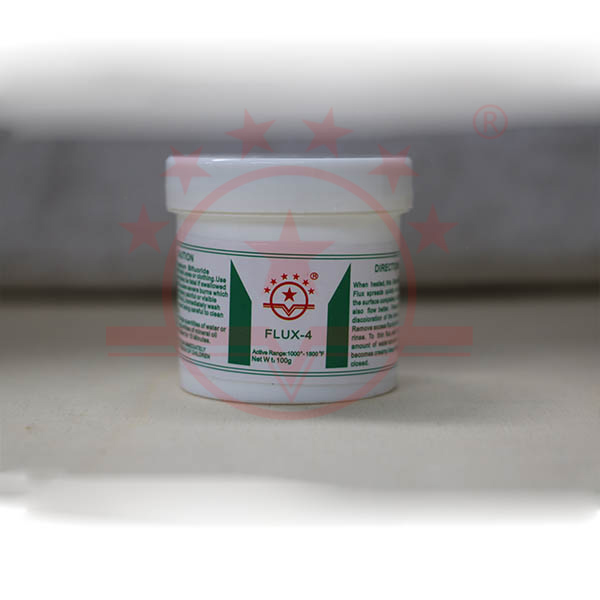
Flux