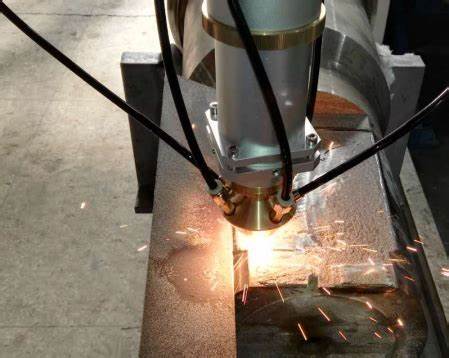
Surfacing welding is an important branch in the field of welding. It is widely used in the manufacture and maintenance of metallurgical machinery, mining machinery, agricultural machinery, petrochemical machinery, transportation, atomic energy engineering and so on.The substance of surfacing is the process of stacking a layer of the same material or different material on the surface of metal parts or rolled metal by means of welding.
In order to give full play to the properties of surfacing alloys, the following aspects should be paid attention to during surfacing:
1. The alloy composition of surfacing layer is the main factor to determine the effect of surfacing welding. The alloy system of surfacing layer must be rationally formulated according to the specific situation, so that the surfacing parts can have a higher service life.
2. Reducing the dilution rate as far as possible is an important starting point for the arrangement of surfacing welding process. Surfacing welding layer generally contains more alloy elements, while the substrate of parts is usually ordinary carbon steel or low alloy steel.Therefore, in order to obtain the desired composition of the surfacing layer, it is necessary to minimize the penetration of the base material into the weld, that is, to reduce the dilution rate.
3) To improve surfacing productivity, surfacing parts are often large in number, and the amount of metal deposited is large, so the surfacing technology with high productivity should be selected.
4) Pay attention to the coordination between the surfacing metal and the base metal. In order to avoid the excessive thermal stress and structural stress caused by the large difference between the surfacing layer and the base metal composition, which causes the cracking and spalling of the surfacing layer, it is required that the surfacing metal and the base metal should have similar expansion, or the solution of the transition layer should be adopted.