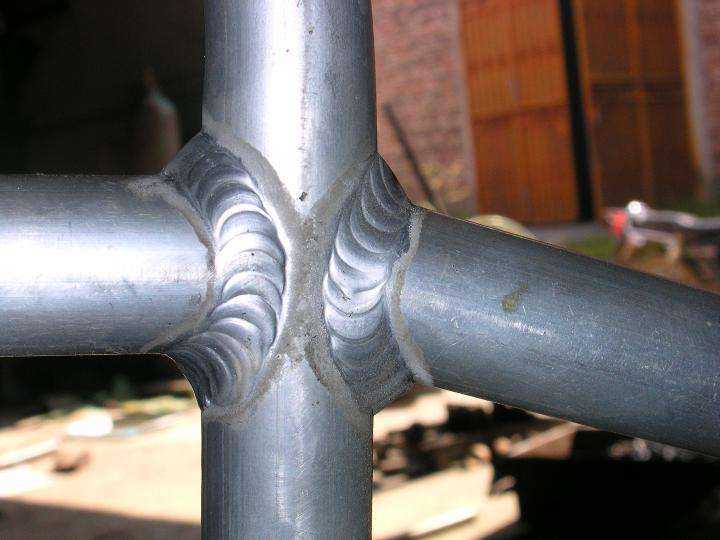
In manufacturing industry, seam welding is mainly used for aluminum and its alloys with a thickness of less than 4mm requiring good air tightness.Due to the good conductivity and thermal conductivity of aluminum alloy, a large welding current must be passed in the welding circuit, so the welding power of welded aluminum alloy is not large, generally about 250 ~ 350kW.
Seam welding is a pair of roller electrodes for relative movement, a welding spot nugget superposition lap joint and seal weld.There are three kinds of seam welding: continuous seam welding, intermittent seam welding and stepping seam welding.Continuous seam welding is the roller continuous power, easy to overheat welding surface, electrode wear is serious, less application.Intermittent seam welding is the continuous rotation of the roller, the intermittent conduction of current, the weld heat affected zone and small, electrode wear.The stepping seam welding is the intermittent rotation of the roller, the current is on when the roller is not moving, it can improve the cooling extrusion condition, the weld quality is good, the electrode life is long.
Intermittent seam welding is usually used in aluminum alloy welding, and stepping seam welding is often used in high strength aluminum alloy welding.Due to the influence of welding spot shunt, the welding current of aluminum alloy seam welding is about 15-50% higher than spot welding, and the electrode pressure is about 5-10% higher. The roller with circular arc section is adopted, and the external water cooling must be forced.
Antirust aluminum has good seam welding property, and it is easy to get good weld, medium strength aluminum alloy and high strength aluminum alloy have slightly worse weld property, but under the condition of clean surface, it is also easy to get satisfactory weld, the weld quality is more stable, and the joint strength coefficient is higher.For example, the strength coefficients of 2AL2-T4, 2024-T3, and 7A04-T6 aluminum alloy joints reach 68.7%, 58.1%, and 59.5%, respectively.
Seam welding and spot welding are similar in structure, but not identical.The metallographic structure of seam welding is the same as spot welding, but after all, seam welding is not simple spot welding repeated, and different areas at the junction often have different structure characteristics.In other words, no obvious columnar crystals were formed between equiaxed crystals of two solder joints due to repeated heating.
The defects of seam welding and spot welding are basically the same, mainly spatter, segregation, loose and crack.Due to the large thermal conductivity and linear expansion coefficient of aluminum alloy itself, and the instantaneous heat input is large when welding seam, so the nugget shrinkage rate is very fast after power failure, and it is easy to cause component segregation, looseness and crack.Therefore, it is necessary to weld in strict accordance with the welding parameters in order to produce high quality aluminum alloy seam welds.