Vacuum brazing furnace, in addition to the vacuum brazing parameters have a serious impact on the quality of brazing joint, the following several important factors also have a great impact on the quality of brazing.
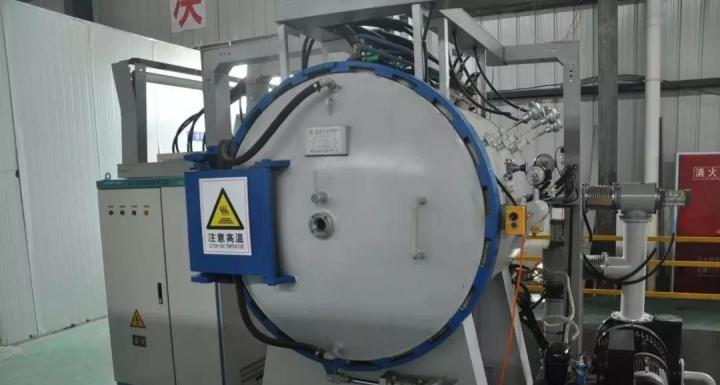
(1) Leakage rate of vacuum brazing furnace
Vacuum brazing furnace leakage rate is one of the important factors affecting the quality of braze welding head, when the vacuum brazing furnace leakage rate is too big, do not conform to the maximum allowable leakage rate there was a leak or vacuum brazing furnace, can cause the oxidation of weldment, therefore, the vacuum brazing furnace gas leakage rate control in maximum allowable leakage rate (usually should be less than 10 ~ 6 pa m3 / S), is very important.
In addition, many domestic vacuum equipment manufacturers, but also use control equipment after the rate, that is, the vacuum system after the main valve closed the furnace pressure rise rate is usually not allowed to exceed 0 ~ 75Pa/h standard, in order to ensure that the furnace should have the minimum leakage rate.
(2) Purity of working gas
In vacuum brazing, argon or nitrogen is usually used as a working gas, which is used both as a forced-cooling gas and as a protective gas against a solder with high evaporative pressure, such as copper or copper alloys.In order to reduce the oxygen content in the gas, the higher the purity, the better. This is because at high temperatures, even the oxygen content is very small, will oxidize the element and make it discolored.
(3) Cleanliness of parts
Surface cleanliness of parts not only before soldering should be performed in accordance with the requirements of oil removal and cleaning process, and also must prevent parts after cleaning oil removal by the secondary pollution, this is because the assembly with solder and furnace charging elbow usually contaminated parts again, so when contact parts wear clean cotton gloves, in order to prevent the parts to pollute again by hand contact.In addition, aluminum hammer is strictly prohibited in assembly to avoid metal pollution of low melting point on brazing surface.Also should pay attention to the stove to contamination of the parts, when just finished copper metallurgical furnace, furnace wall there will be more or less copper pollution (during using the argon adjust the pressure in the furnace, copper solder few volatile, but it is impossible to completely avoid), if then, more or less have copper pollution (during using the argon adjust the pressure in the furnace, copper solder few volatile, but it is impossible to completely avoid), if then brazing nickel base material parts, may cause copper dissolution of nickel, so deal with empty furnace vacuum cleaning, pollution of the furnace wall of low melting point alloy volatile again, and pumps.
(4) Clearance size during assembly
The size of the joint clearance can directly determine the density and strength of the brazing joint. Too large clearance can weaken the capillary action, make filling of the filler metal difficult, weaken the alloying action, and lead to poor mechanical properties of the joint.Especially for open joints with two ends, the surface tension of liquid solder and parts is less than the gravity of the solder, the liquid solder cannot maintain its own mass, resulting in the failure of brazing.The gap is too small and will hinder the filling of the filler metal, making it difficult to form a joint with good penetration rate. The surface tension between the liquid filler metal and the parts is less than the gravity of the filler metal, and the liquid filler metal cannot maintain its own quality, leading to the failure of brazing.The gap is too small and will hinder the filling of the filler metal, so it is not easy to form a joint with good penetration rate. However, the smaller the brazing clearance is, the better, on the premise of not affecting the filling of the filler metal.In this way, the alloy of the solder is stronger, which is conducive to diffusion, and there are fewer metal compounds. More importantly, when the solder in the narrow gap is subjected to plastic deformation by the brazing metals with high strength around it, complex stress is formed in the joint, resulting in a great increase in the joint strength.
In production practice, joint clearance is guaranteed by machining accuracy, and is generally not reinspected.For brazing stainless steel and stainless steel with copper and copper alloy filler, the assembly clearance is 0.03 ~ 0.10mm (the same thermal expansion coefficient of the same material, the assembly clearance is also the brazing clearance). For brazing high wet alloy with nickel base filler filler, the assembly clearance is 0.013 ~ 0.076mm.