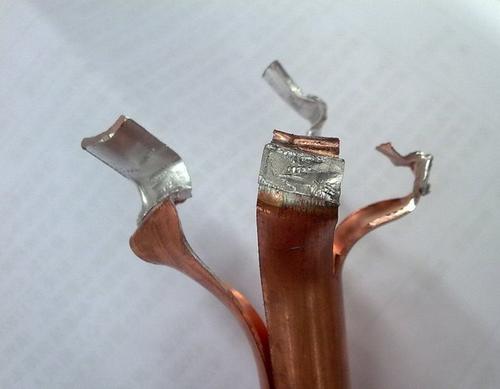
Both cold pressure welding and hot pressure welding are a form of pressure welding. The whole process of cold pressure welding is carried out at room temperature, but the deformation degree of cold pressure welding is large and the welding pressure is relatively large.Under external pressure, the oxide film on the contact surface between the welding parts is broken and extruded by the plastic flow of the metal interface, so that the clean metal is in close contact, and the interatomic combination is achieved, and finally the solid welding joint is formed.
Among hundreds of welding methods, cold pressure welding is the lowest welding temperature.The pressure of cold pressure welding is generally higher than the yield strength of the material, and the amount of deformation generated is about 60 ~ 90%. The pressure method is generally slow pressure, rolling pressure, impact force and so on. It can also be divided into several times to achieve the required amount of deformation.Cold pressure welding does not produce the softening zone, heat affected zone and brittle mesophase common in other welding joints, so it is especially suitable for heat sensitive materials, materials easily oxidized at high temperature, and some dissimilar metal materials (Cu, Al, Au, Ag, Ni, Zn, Ti, Pb and their alloys).
According to the form of the joint, cold pressure welding is divided into lap cold pressure welding and butt cold pressure welding two types, lap cold pressure welding can weld 0.01 ~ 20mm foil, strip and sheet, tube end and bar lap can also be welded by lap cold pressure welding.When lap cold pressure welding, generally use steel pressure head for pressure, pressure head type: columnar pressure head for cold pressure spot welding;Roller pressure head for cold pressure weld welding;Cold pressure welding butt-welding of clamp head.In the actual production of cold pressure welding, the degree of plastic deformation necessary for cold pressure welding is determined by the mold. As long as the welding pressure is large enough and the surface cleanliness and roughness of the welding parts meet the requirements of cold pressure welding, the welding quality can be guaranteed.
Two, welding operation
The cold pressure welding of copper and aluminum is achieved at room temperature by top forging plastic deformation of 80%, so there is no intermediate brittle compound of copper and aluminum.Due to the local flow deformation of the solid surface of copper and aluminum itself (Cu/Al = 1∶0.7), the effective interatomic bonding is formed and finally becomes a whole, which improves the contact thermal conductivity and electrical conductivity of the copper-aluminum welding joint. Butt joint and lap joint are mostly used in the cold press welding joint of copper and aluminum.
The butt cold pressure welding of copper and aluminum, firstly remove the oil scale and other impurities on the surface of copper and aluminum, and then process the contact end face of copper and aluminum into regular, flat geometric size, especially the symmetric axis of copper and aluminum welding parts is not bent.The processing of the end face usually adopts mechanical processing method. Before welding, the copper and aluminum should be annealed to soften them and increase the plastic deformation ability of the welding parts, which is also an important measure to improve the welding quality.Copper and aluminum bars are usually welded in this way.
Copper and aluminum lap cold pressure welding, first of all, the surface of the copper and aluminum welding parts to be cleaned, there can be no stains and impurities, and then the workpiece is assembled between the jig, and pressure on the upper and lower head, so that copper and aluminum parts each produce enough plastic deformation to form a solder joint.This form of cold pressure welding can be single-sided, also can be double-sided;The shape of solder joint is round, rectangular or square, special shape;The diameter of circular solder joints is D = (1 ~ 5) δ, the width of rectangular solder joints is B = (1 ~ 1.50) δ, and the length is L = (5 ~ 60) B.
If the thickness of copper and aluminum welding parts is very different, the single-side deformation method can be used for welding. In this case, the diameter of the original solder joint is D = 2δ, and the size of the rectangular solder joint is width B = 2δ and L = 5B.If multi-spot welding, should be cross-distributed, solder center distance should be greater than 2 times the diameter of the head, rectangular solder joints should be significantly skewed distribution.
It is worth mentioning that the conditions of use: copper and aluminum cold pressure welding head, the temperature rise of short-term use (within 1h) should be limited to below 300℃;The temperature rise of long-term use is not more than 200℃.