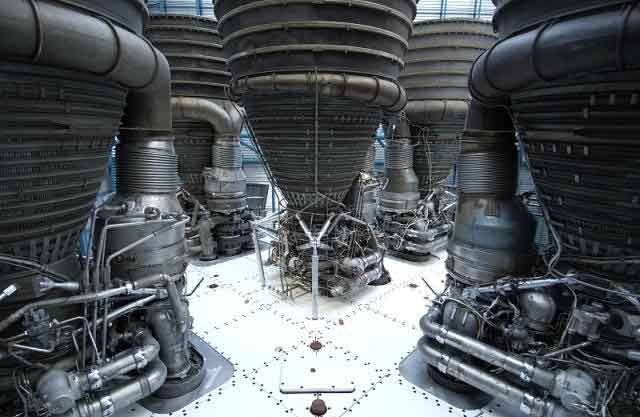
In the 1990s, the new large thrust hydrogen-oxygen engine used in China's main rocket, the Changsanjia series of launch vehicles, encountered large nozzle welding problems. One of the difficulties is that the entire weld length of the sandwich nozzle is nearly 900 meters, the nozzle tube wall is only 0.33 mm, and the welding gun stays for 0.1 second, which may burn the tube or weld.
At that time, the welding technician Gao Fenglin used his own technology and experience for more than a month to complete the manual welding of the large nozzle.
The rocket engine is the most important group component of the rocket, and it is called the rocket "heart". The nozzle is located in the rocket engine thrust chamber and is responsible for converting the thermal energy of the high temperature and high pressure gas generated by the propellant combustion into kinetic energy, which directly affects the specific impulse performance of the engine.
In recent years, commercial aerospace has accelerated development, and low-cost, short-cycle, and mass-produced production has gradually become the pursuit direction. Manual welding, which takes several months of production cycle and high dependence on expert technicians, does not meet the market demand for mass production. Rocket companies began to explore robotic welding processes.
Recently, the private aerospace company Beijing Blue Arrow Space Technology Co., Ltd. (hereinafter referred to as "Blue Arrow Space") announced a laser welding sandwich nozzle process, laser welding by robots. At present, the "Tianjin" (TQ-12) 80-ton engine nozzle using this process has been successfully launched.
According to the Blue Arrow Aerospace staff, the TQ-12 engine nozzle has a diameter of more than 1 meter and is laser welded by a robot for only two days. As the subsequent process matures, welding time or compression to within 10 hours, the manufacturing cycle and cost are only about 1/10 of the conventional nozzle manufacturing process.
TQ-12 is the first 80-ton liquid-oxygen methane engine developed by Blue Arrow. The design of the thrust chamber was completed in March last year. Six months later, the 20-second short-range ignition test of the short nozzle thrust chamber was completed. In January of this year, the TQ-12 gas generator completed the first round of ignition test.
In the working process of the large thrust liquid rocket engine, the nozzle needs to withstand the intense high temperature heating of the gas, and the heat per square meter is close to the surface of the sun. The best high-temperature resistant metal materials currently in control of humans cannot withstand such huge heat flows.
Therefore, the engineers made the structure of the nozzle into a sandwich, allowing the propellant to flow at high speed in the interlayer before entering the combustion chamber, taking away heat, thereby ensuring that the nozzle is not burned.
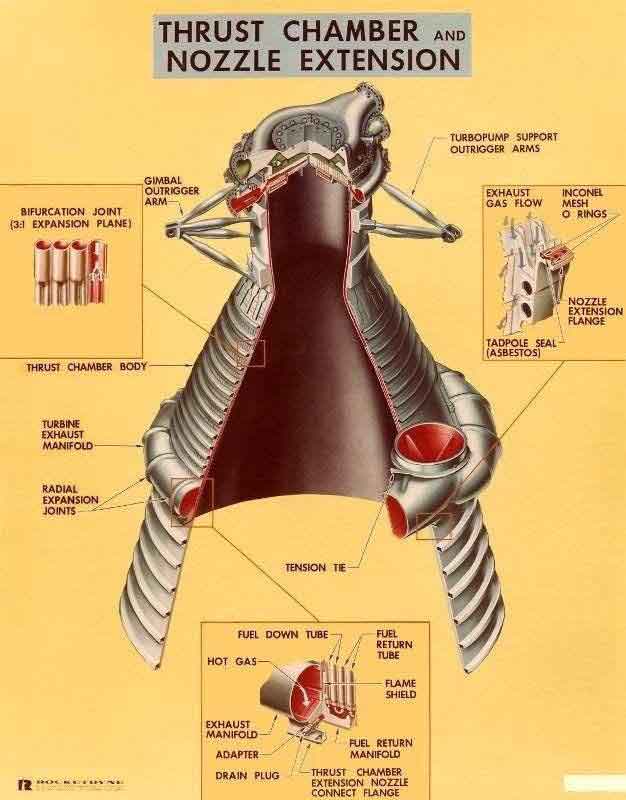
Rocket engine nozzle schematic picture Source: Network This kind of regenerative cooling nozzle needs to have sufficient structural strength and rigidity to withstand the axial thrust of the engine, internal hydraulic pressure, strong vibration; also need to be light enough weight to improve the engine Push-to-weight ratio; and optimal profile accuracy to allow the gas to expand in an optimal manner to achieve the highest specific impulse.
In the current engineering applications, the sandwich nozzle structure mainly has three types: corrugated plate type, milled groove type and tube bundle type.
Among them, the tube bundle structure is divided according to the arrangement of the tubes, and can be divided into an in-line type and a spiral type. The Blue Arrow Aerospace uses a spiral tube bundle structure. Hundreds of alloy tubes with a wall thickness of about 3 mm are welded together in such a way as to change the helix angle.
Schematic diagram of cross section of nozzle: Source: Network “We not only need to consider the maturity of the technology itself, but also the supply of equipment for this process. Whether the manufacturing cost is low, whether the development cycle is short enough, and whether standardization and automation can be achieved. Whether it is energy saving and environmental protection, etc., said Yuan Yu, senior engineer of Blue Arrow Aerospace.
After comparing and analyzing various processes such as vacuum pressure brazing, diffusion welding and laser welding, and researching related equipment companies, the research team of Blue Arrow Aerospace finally selected the laser welding sandwich nozzle process.
The process has a number of advantages, including high weld strength, high pressure bearing capacity, high degree of automation, fast welding speed, and operation in the atmosphere. However, before this, there is no research basis for this technology in China, and there are no mature products of related models in the world.
The robot is welding the rocket engine nozzle. Source: Blue Arrow Aerospace Yuan Yu said that in the past year or so, the research team has started from the most basic welding tests and completed a number of tests. In order to solve the deformation and displacement problems in the nozzle welding process, the welding sequence and process parameters were adjusted several times to find the optimal solution. "Next, our job is to weld more, accumulate more data, expose and solve potential problems as soon as possible." Yuan Yu said.
Rocket Engine Nozzle Image Source: Blue Arrow Aerospace
Blue Arrow Aerospace has now cooperated with the Laser Equipment Manufacturing Group to build a complete set of robotic laser welding equipment. Fully automatic laser welding is achieved by using a large nozzle robot.
The equipment has a maximum welding power of 8000 watts, a maximum weldable depth of 10 mm, and a maximum weldable diameter of nearly 2 meters. It is suitable for welding of various stainless steels, high-temperature alloys, aluminum alloys, copper-steel dissimilar metals, etc.