Identification of an application’s function, selection of materials, definition of an application’s shape, and selection of an appropriate brazing process are the four essential engineering decisions contributing to a successful brazing operation. If there is a problem with your brazing operation, it can be avoided or resolved by manipulating any of the four aforementioned variables.
Usually, a brazing process can be supported by a number of possible brazing processes, but only one of the possible options is superior, whether for technical reasons or economic feasibility. Hypothetically, an automotive rotor assembly could be brazed by dip, furnace, torch, or induction; engineers must evaluate the risks and benefits associated with each method, considering all precedents and available measurable data about each process. Much weight is given to what is commonly known as the “Precedent of Similar Application”, and as such, most engineers would quickly discern that either dip brazing or furnace brazing would be appropriate due to the shape/design of the application. However, this precedent can never take the place of employing methodology applying appropriate engineering principles (heat transfer, metallurgy, fluid dynamics, etc.). Difficulties in braze process development can frequently be traced back to failure to apply proper engineering principles.
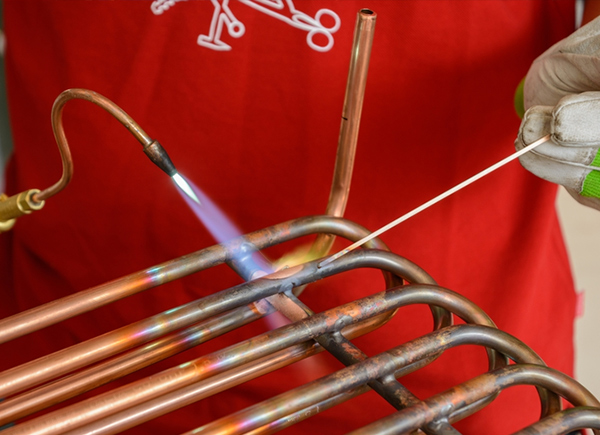
Development of a braze process must be deconstructed into separate steps or stages. As this process enters the fabrication and testing of a prototype, it is wise to proactively employ PFMEA (process failure modes and effects analysis) to prioritize and address risks rather than having to react to a failure after it becomes evident. Once a sound process is established, maintaining repeatability and quality of production output is easily achieved by insuring brazing equipment is functioning at its highest levels. Following the OEM’s recommended maintenance schedule, communicating the schedule to braze operators, and requiring them to adhere to that schedule will help to insure positive production results.
Xinxiang Qixing Welding Material Co., Ltd started in the 1980’s, we are the famous Chinese professional company, which are specialized in research development and sale brazing materials,we always promise “best quality, best service!” Keep strive to make "QIXING" brand brazing filler metal to be the most welcomed products in China and the whole world! If you have any problem with brazing process,just contact us.