I'm talking about manual welding, with electrodes
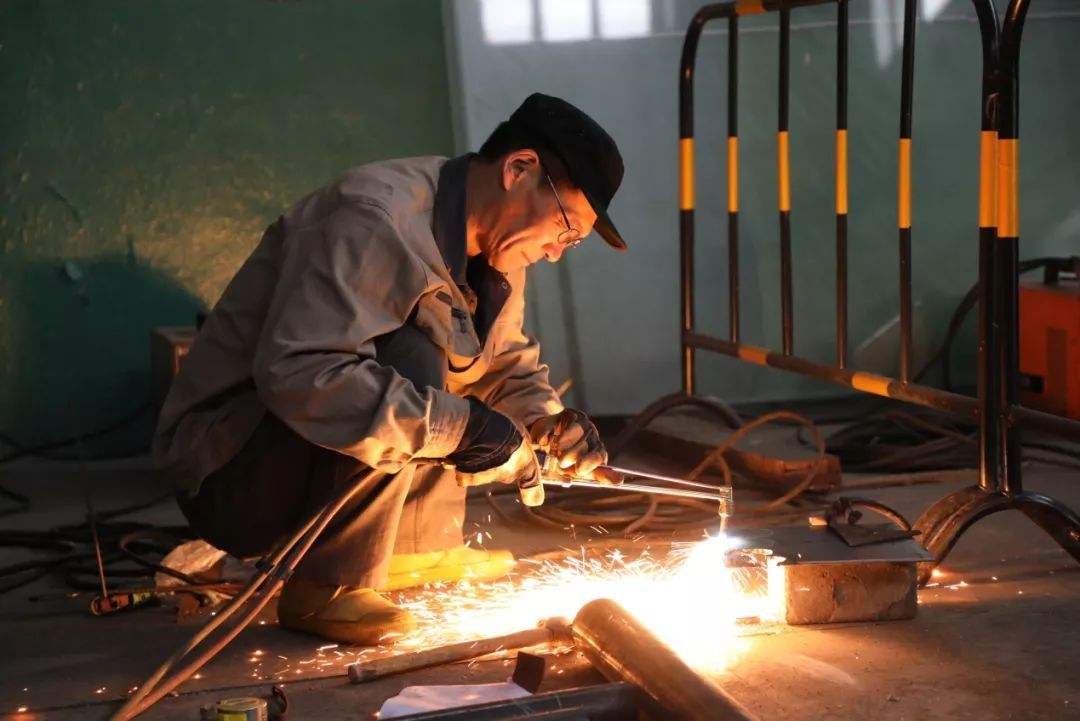
Manual welding, or manual arc welding, is a manual welding method that USES the arc as a heat source to melt the electrode and the base material to form the weld line.According to manual arc welding process standard, it mainly includes four welding methods: flat welding, vertical welding, horizontal welding and overhead welding:
(1) flat welding
1. Select qualified welding process, electrode diameter, welding current, welding speed, welding arc length, etc., and verify by welding process test.
2. Clean the welding joint: check whether the groove and assembly gap meet the requirements before welding, whether the positioning welding is firm, and there shall be no oil or rust around the welding seam.
3. The baking electrode shall conform to the specified temperature and time. The electrode taken out from the oven shall be placed in the electrode heat preservation bucket and taken out at any time.
4. Welding current: select the appropriate welding current according to factors such as welding thickness, welding level, electrode type, diameter and welder's proficiency.
5. Arc initiation: the starting and dropping point of fillet weld shall be at the end of the weld, which should be more than 10mm, and no arc shall be randomly struck. After the arc initiation, the welding rod shall be pulled away from the welding seam area immediately, so as to maintain a gap of 2 ~ 4mm between the welding rod and the member and generate arc.Butt weld joint in time and Angle joint weld, on both ends of weld arc plate and lead plate, must again after the arc board arc welding to weld zone, midway joint should be ahead of the weld joint of 15 ~ 20 mm in flint arc, will weldment preheating before welding rod back to the start of weld, the molten pool to fill the requirements after the thickness of the weld can move forward.
6. Welding speed: it is required to weld at a constant speed to ensure uniform thickness and width of the weld. It is advisable to maintain an equal distance (2 ~ 3mm) between molten iron and slag in the melting pool from inside the mask.
7. Welding arc length: according to different electrode types, the arc length is generally required to be stable, acid electrode is generally 3 ~ 4mm, alkaline electrode is generally 2 ~ 3mm is appropriate.
8. Welding Angle: according to the thickness of the two welds, there are two aspects of the welding Angle, one is the Angle between the electrode and the welding direction is 60 ~ 75°;Second, there are two cases of welding rod and welding about the included Angle, when the thickness of the welding piece is the same, the included Angle of the welding rod and welding piece are 45°;When the weld thickness is not equal, the Angle between the electrode and the side of the thicker weld should be greater than the Angle between the electrode and the side of the thinner weld.
9. Arc closing: after each weld is welded to the end, the arc pit shall be filled, and the arc shall be taken in the opposite direction of the welding direction, so that the arc pit is thrown into the weld pass to prevent the arc pit from biting the meat.After welding, the arc plate shall be cut off by gas cutting, and the arc plate shall be repaired and ground flat, and shall not be shot down by hammer.
10. Slag removal: the slag shall be removed after the welding of the whole weld, and no problem shall be found after welder's self-inspection (including appearance and weld size, etc.), before the welding can continue at the transfer site.
(2) vertical welding: the basic operation process is the same as that of horizontal welding, but the following problems should be paid attention to:
1. Under the same condition, the welding power supply is 10% ~ 15% less than the welding current.
2. Adopt short arc welding, the arc length is generally 2 ~ 3mm.
3. The Angle of welding rod is determined according to the thickness of welding parts.The thickness of the two welds is the same, and the Angle between the electrode and the left and right direction of the electrode is 45°;When the thickness of the two welds is different, the Angle between the electrode and the thicker side of the welds should be greater than the Angle on the thinner side.The electrode shall form an Angle of 60° ~ 80° with the vertical plane, so that the Angle arc is slightly upward and blown to the center of the molten pool.
4. Arc recovery: when the welding reaches the end, fill the arc pit with arc exhaust method and move the arc to the central stop of the melting pool.Do not throw the arc pit aside.In order to prevent bite, the arc should be reduced to change the electrode Angle, so that the electrode and welding piece vertical or slightly by the arc downward blowing.
(3) horizontal welding: basically the same as flat welding, the welding current is 10% ~ 15% less than that of the same condition, the arc length is 2 ~ 4mm.Welding rod Angle, horizontal welding electrode should be downward tilt, its Angle of 70° ~ 80°, to prevent falling molten iron.According to the thickness of the two welding pieces, the Angle of the electrode can be adjusted appropriately. The forward direction of the electrode and welding is 70° ~ 90°.
(4) inverted welding: basically the same as vertical welding, horizontal welding, its electrode and welding part of the included Angle and welding part thickness, the electrode and welding direction into 70° ~ 80° Angle, it is appropriate to use small current, short arc welding.