Generally brazing and silver welding is more common, although called brazing silver welding, but in fact the main component is not metal!The development of aluminum alloy welding technology is different from carbon steel.Since there are many elements in the original aluminum alloy and each alloy element has different effects on the weldability of the base material, it is necessary to develop many different filler alloys to adapt to these different alloy elements.For example, some primary aluminum alloys have special chemical properties, are designed for specific mechanical and physical characteristics, and do not have the best weldability.
The chemical properties of these alloys are not good and easy to produce solidification cracks.In order to develop suitable welding process without producing crack weld, it is necessary to know the solidification crack sensitivity of each different alloy.This welding development is a big project in itself.Much of the work is done by aluminum base manufacturers, because they know the reliable welding methods and processes of aluminum, and also by aluminum assemblers, who know the potential of this new material and are eager to use it.Two pioneers in the development of welding in the United States were ALCOA (American aluminum company) and Kaiser aluminum chemical company, both of which have publications;Welding ALCOA aluminum was first published in 1954 (see figure 1) and welding Kaiser aluminum was first published in 1967.
In the age of competition in the modern industrial world, structural metals must be weldable.The first welding technologies suitable for aluminum include hydroxyl fuel gas welding and resistance welding.Aluminum arc welding is mainly limited to SMAW (manual arc welding), sometimes called MMA.This welding process USES a tubular electrode.It soon became clear that the process was not optimal for welding aluminum.One of the main problems is the corrosion caused by flux residue, especially in filler welds, where flux remains in the weld and promotes weld corrosion.
The breakthrough in aluminum as a structural metal came with the advent of inert gas welding in the 1940s.For example, GMAW (gas metal arc welding), also known as MIG (melted inert gas arc welding);GTAW (gas tungsten arc welding), also known as TIG (gas inert gas arc welding).With the current use of inert gas in the welding process of molten aluminum, it is possible to produce high quality, high-bearing welds at high speeds and all directions, without corrosive flux.
Today, various techniques and welding processes are used to make aluminum and aluminum alloys weldable.Two recent processes are laser beam welding (LBW) and friction stir welding (FSW).However, GTAW/TIG and GMAW/MIG welding processes are still the most popular.
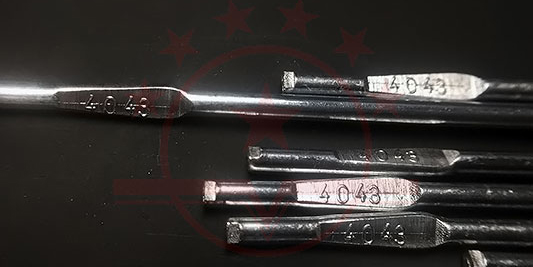
aluminum alloy welding wire